«SMNPO – Engineering» JSC, founded in 1896, is now one of the largest machine-building enterprises in Europe manufacturing equipment for oil, gas and chemical industries.
Our Resources
- 4 product-focused manufacturing sites:
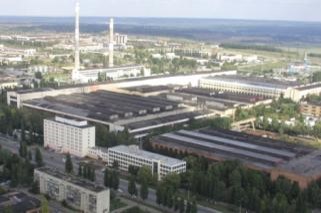
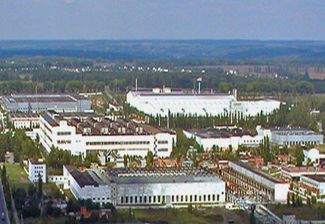
Pumping manufacturing site specializes in producing of pumping equipment for Nuclear Power Plants
The first reactor coolant pump GCN-195 M for NPP with power units VVER-1000 was manufactured in 1981. This was a qualitatively new type of equipment for Sumy engineeres.
At present, the pumping manufacturing site has mastered and produces a large range of feed and condensate pumps of the second circuit of nuclear power plants with a wide range of flows and heads, as well as special pumps for creating circulation in a closed cooling circuit and purifying the purge water of the main circuit of the steam generator, for supplying water to the seals of the reactor coolant pumps, etc.
Nuclear power plants in Ukraine, Russia, Armenia, Bulgaria, China, India and other countries operate with pumping equipment made by the company.
All pumping equipment is tested at a centralized testing complex with unique full-scale benches.
The pumping manufacturing site has more than 130 units of metal-cutting equipment, including 16 CNC machines, 6 machining centers with a high degree of technological accuracy, Deuma automated welding machines with manipulators of of up to 100 tons lifting capacity, crane equipment with a lifting capacity up to 150 tons, laboratories for all types of tests, X-ray installations, including the linear electron accelerator LEA.
The Fixed Equipment Manufacturing Site is the oldest one in the Company. It dates back to 1896.
The equipment of stainless and carbon steels, titanium alloys, hastelloy, zirconium and other materials is manufactured In five workshops of the site. They produce here tanks, columns, reactors, heat exchangers, evaporators, pumps and compressors, centrifuges and separators for various industries.
To manufacture over-sized products (columns, heat exchangers and tanks), the workshops are equipped with powerful presses, various rollers, including of Heusler company (Switzerland) for rolling sheets up to 120 mm thick, a set of equipment for flanging bottoms and obtaining ribbed pipes and coils of various shapes , the complete line for the production of spiral heat exchangers, various equipment for expanding pipes in tube sheets of heat exchangers, incl. chambers for electric pulse flaring.
The workshops are equipped with modern metal-cutting equipment, as well as with CNC. For the high-precision parts processing Max-Muller, Forest, Kolb and other machines are used. The body parts are manufactured on high-precision horizontal boring and coordinate boring machines.
There is a specialized gear cutting facility for the manufacture of high-precision spur and helical cylindrical gears of the 4th degree of accuracy with a diameter of up to 1500 mm. The site is equipped with equipment manufactured by the world’s leading companies: Pfauter, Hoffler, Lorenc, Safop, etc.
The rotors are balanced on Schenck (Germany) high-precision balancing machine.
The electroslag and automatic submerged arc welding are widely used in the workshops. Robotic and automated welding units of Deuma (Germany), IGM (Austria) allow welding products weighing from 10 to 100 tons. There are electron beam welding units.
The quality of products is confirmed by laboratory tests, X-ray examination, ultrasonic flaw detection, hydrotesting.
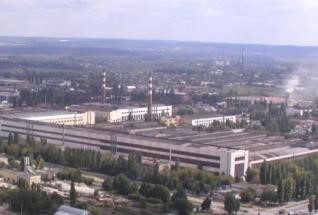
- Over 5,000 production staff
- 360 duly qualified design & engineering staff
- Subsidiary engineering company “NEFTEKHIMPROEKT”, 160 staff performing project documentation development
- 150 installation & commissioning team performing, installation, commissioning and equipment maintenance
- Scientific-and-testing facilities, including the only in Europe unique GPU full load string test bench by natural gas
- Over 2500 machinery units & 800 CNC centers
- Modern forging and pressing equipment, including JSW (Japan) press with an effort of 2000 tons and the only in Ukraine Wagner Dorthmund (Germany) ring rolling machine
- Cranes with lifting capacity up to 150 t, indoor & outdoor railway infrastructure
- Company’s total area is more than 200